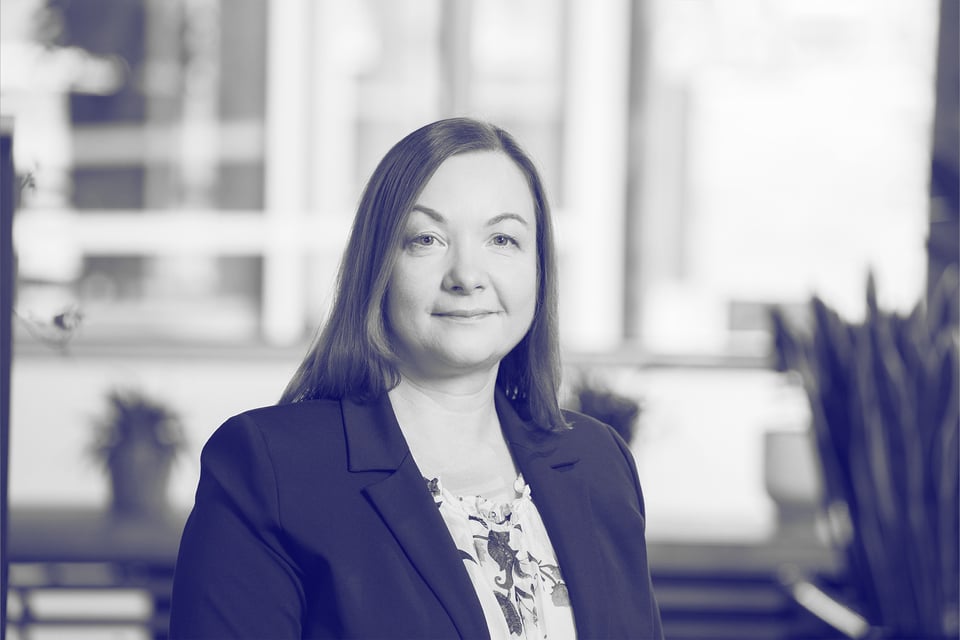
Once we got our final response that our lab had been accredited with ISO 17025, I was relieved and tired. I was also grateful to the entire Biosafe team for their contribution to the significant amount of quality work needed to achieve this goal. I wanted to tell what the journey was like for everyone who has a similar path ahead of them.
Everything seems great at first
When I initially started work at Biosafe as a pair of hands in the laboratory, I was convinced of the quality of the lab’s work. Sample handling and method protocols were carefully instructed. Every researcher like me, after general familiarization and orientation with each individual lab method, could start independent work with confidence according to written instructions. You could always ask a more experienced colleague for help too.
I had started work with customers as a project manager when I was asked if I was willing to make sure our quality standards are where they ought to be. Biosafe's quality work had previously been a part-time job. I was really excited about the opportunity to take our already top-notch quality work to an even higher level.
Finding out what ISO 17025 really requires
As I became more familiar with the ISO 17025 laboratory accreditation standard (officially ISO 17025:2017 General requirements for the competence of testing and calibration laboratories), I and other quality group members who were primarily involved in quality documentary work with me noticed that we had a lot of documentation work ahead of us before we could apply for accreditation. Some things hadn't ever been documented.
Laboratory research was naturally all up to standard, but ISO 17025 also requires documenting for example people’s skills and operating culture. Since we were an organization of only a few people, much of that information existed only in the minds of managers. So, because it was not documented, it didn't exist from a standard perspective. There was also little written guidance on administration, quality assurance and procurement.
Make time for a lot of documentation
We set ourselves the goal of going over every requirement in the ISO 17025:2017 standard and creating documentation to get a common understanding of how we have agreed to do things. We worked and learned together. There were times when customer work or a problematic case in the laboratory took a lot of time and the documentation slowed down. We had to postpone the application deadline from our original goal too. However, at no point did we give up on our goal of becoming accredited. Our original idea was also to apply for accreditation for several methods at the same time, but in practice, it proved sensible to focus on one method in the initial application and extend the accreditation later if deemed necessary.
You can design how your quality guidelines are done, just make sure you have them
ISO 17025 does not provide any precise guidelines for laboratories on how to document a particular matter, but it does contain requirements for laboratories to demonstrate they operate competently and are able to generate valid results. Laboratories that conform to ISO 17025 will also operate generally in accordance with the principles of ISO 9001. Sometimes it was challenging to agree on what kind of documentation some functions needed to meet the requirements of the standard. We asked external quality management experts to conduct internal audits at Biosafe to gain an external view of the level of our documentation. In some cases, we also found that our policies needed to be updated to comply with the spirit of the standard. Although our methodological guidelines were updated with this work, the methods we use in the lab have not changed (unless EFSA's requirements or the standard followed in the method have changed).
Most of the quality work happens long before submitting the application
Finally, we were ready to submit our application for accreditation. I was gratified when I sent FINAS (Finnish Accreditation Service; the national accreditation body in Finland) an email to inform we had submitted our application to their system. However, I knew that before we get the accreditation decision, there was still a long way to go and a lot to do. It would take FINAS time to familiarise themselves with our materials, so the audit would not be until about six months after the application was submitted. After that, we would have three months to make corrections. And if necessary, additional corrections will be made on a short schedule thereafter.
After minor additional corrections, we were notified that our application for accreditation has been approved. I felt an overflowing relief for all of us at Biosafe and I was happy for our customers too: the reason for this great effort was to give our customers the peace of mind of knowing they are in verifiably safe hands.
The quality work continues.
Read more about what ISO 17025 meaning and standards from our article Biosafe has an ISO 17025 accredited laboratory.
|
Read more:
Microbial testing – An overview of what it is and what it is for »
Topic:
Author: